工作機械でMCナイロンを加工する際の最適な切削条件とは
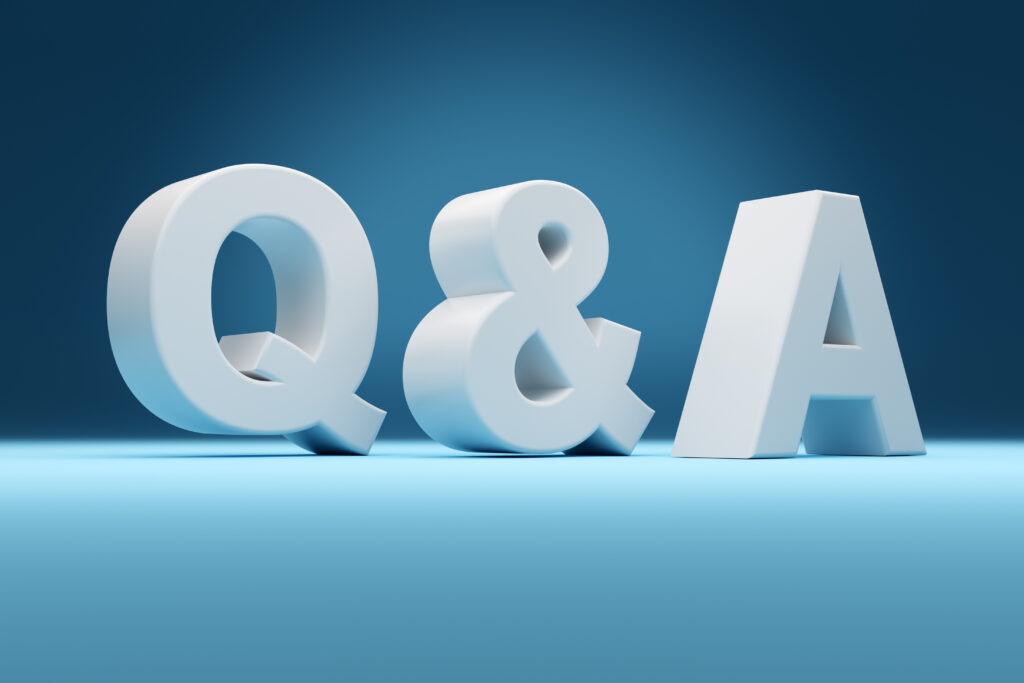
工作機械でMCナイロンを加工する際、最適な切削条件を知っていますか?MCナイロンは耐摩耗性、潤滑性、機械的性質など優れた特性を持つ素材ですが、適切な切削条件を知らないと加工効率が低下したり、工具の寿命が短くなることがあります。本記事では、MCナイロンの切削条件に焦点を当て、効率的な加工方法について詳しく解説します。加工業界に携わる方や工作機械に興味がある方にとって、貴重な情報となることでしょう。加工効率を向上させ、品質の高い製品を生産するために、最適な切削条件について一緒に学んでいきましょう。
MCナイロンとは
MCナイロンの特性
特性 | 詳細 |
---|---|
耐摩耗性 | 摩耗に対する抵抗力が高く、長期間使用しても劣化しにくい。 |
耐衝撃性 | 衝撃や振動に強く、壊れにくい。 |
機械的強度 | 高い引張強度と圧縮強度を持ち、重荷重に耐える。 |
化学薬品耐性 | 多くの化学薬品に対して耐性があり、化学工業での使用に適している。 |
加工性 | 切削や成形が容易で、精密な部品製造に向いている。 |
熱変形 | 熱に弱く、過度な温度変化により変形しやすい。 |
最適な切削条件
- 切削速度: 低めの切削速度を設定することで、発熱を抑え、加工中の変形を防ぎます。
- 送り速度: 適度な送り速度を選ぶことで、切屑の除去をスムーズにし、表面仕上げの質を向上させます。
- 冷却液: 冷却液を使用して加工面の温度を一定に保ち、工具の摩耗を減少させます。
工作機械におけるMCナイロンの利用
工作機械でMCナイロンを加工する際、適切な切削条件を見極めることは極めて重要です。MCナイロンは耐摩耗性や耐衝撃性に優れており、機械部品などへの利用が広がっています。適切な切削条件には、刃の種類や速度、フィードレートが含まれます。例えば、シャープなエッジを持つカーバイド製の刃は、MCナイロンの滑らかな切断面を実現するのに効果的です。また、過度な熱が生じないように低~中速の切削速度を維持することが肝心です。さらに、均等なフィードレートを保つことで、切断面の精度を向上させることができます。これらの条件を守れば、MCナイロンの加工はより効率的で品質の高いものとなるでしょう。最後に、一貫した切削条件の適用は、工具の寿命を延ばすと共に、コストパフォーマンスの面でも利点があります。
MCナイロンの旋盤加工の基礎
旋盤加工とは
工作機械でMCナイロンを加工する際の最適な切削条件を見極める事は、製品品質と加工効率に大きく影響を及ぼします。MCナイロンは、耐摩耗性や耐薬品性が高く、工業部品など多方面で用いられる工業用プラスチックです。最適な切削条件とは、切削速度、送り速度、切り込みの深さ、刃の形状などが適切に設定され、MCナイロンの特性を活かしながら無駄なく加工を行うことです。
例えば、切削速度はMCナイロンの熱に対する弱さを鑑みて低めに設定します。送り速度や切り込みの深さについても、材料が変形したり、溶けたりしないよう注意深く選ぶ必要があります。また、刃の形状はMCナイロンの滑らかな表面を残すのに最適なものを選び、切削工具の材質についても、耐摩耗性に優れたものを使用することが勧められます。
これらの切削条件を適切に設定することで、MCナイロンは高品質で精度の高い加工が可能となり、無理な負担を加工機械に与えることなく、効率的な生産を達成できます。最適な切削条件を見定め、賢く加工を進めることが、工業分野におけるMCナイロンの可能性を最大限に引き出す鍵となるのです。
MCナイロン旋盤加工における一般的な不安要素
熱管理の重要性
要素 | 説明 |
---|---|
熱への感受性 | MCナイロンは熱に弱く、切削時に熱が問題となる |
切削速度 | 低〜中速が推奨され、過度な熱の発生を防ぐ |
冷却方法 | 切削液の使用により熱の発生を抑え、工具の摩耗を防ぐ |
加工精度の向上
要素 | 説明 |
---|---|
弾性変形 | MCナイロンは弾性があり、加工中に変形しやすい |
送り速度 | 低い送り速度で加工精度を向上 |
切削条件の選定
- 熱管理: 切削速度と冷却方法を適切に設定することで、熱の発生を抑えます。
- 加工精度: 低い送り速度を用いることで、変形を最小限にし、精度の高い加工が可能になります。
これらの条件を守ることで、高品質なMCナイロン製品の加工が実現できます。
MCナイロンの旋盤加工での切削条件の重要性
MCナイロンは、その優れた強度と耐摩耗性から多種多様な工業分野で利用されています。特に工作機械を用いた加工時における適切な切削条件の選定は、高品質な製品を効率良く生産するために不可欠です。最適な切削条件では、MCナイロンの加工精度が向上し、摩耗や亀裂のリスクを低減させることができます。例えば、適正な切削速度の選定は、材料の発熱を抑え切削時の変形を防ぎます。また、適当な送り速度と切り込み深さの設定も、製品の寸法精度や表面粗さを保つ上で重要です。さらに、潤滑剤の使用は、切りくずの排出を促進し刃物の摩耗を防ぐ役割を果たします。このように、MCナイロンの加工においては、切削速度、送り速度、切り込み深さ、そして潤滑の各条件が総合的に検討されるべきです。最終的に、適正な切削条件を見極めることは、コスト削減と生産性の向上に直結し、加工品質を一層高めることに貢献します。
MCナイロンの最適切削条件の理解
切削速度の設定
切削速度の重要性
要素 | 説明 |
---|---|
MCナイロンの特性 | やわらかい材質であり、適切な切削速度の設定が重要 |
高すぎる切削速度 | 材料が溶けて精度が落ちる可能性がある |
低すぎる切削速度 | 加工時間が過剰にかかり、生産性が低下する |
推奨される切削速度
切削速度範囲 | 説明 |
---|---|
50〜200 m/min | 一般的な推奨範囲。ただし、MCナイロンの種類や加工機の特性により調整が必要 |
切削条件の最適化
- 切削速度: 材質の特性に合わせて適切な速度を選定することが、加工の効率と精度を高めます。
- 冷却剤の使用: 適切な冷却剤の使用により、熱の発生を抑え、加工面の品質を維持します。
- 刃物の選定: 刃物の選定も加工品質に大きな影響を与えるため、注意が必要です。
最適な切削速度を設定し、冷却や刃物の選定を適切に行うことで、MCナイロンの加工効率と品質を高めることができます。
送り速度とは
送り速度は、MCナイロンを工作機械で加工する際に最適な切削条件を設定する上で重要な要素です。適切な送り速度を見極めることで、効率良くかつ精度の高い加工が可能になります。MCナイロンは熱に弱く、また切りくずの排出も考慮しなければならないため、高速すぎると溶けたり、形状が変わる可能性があります。反対に、送り速度が遅すぎると、工具の摩耗が早まり、加工コストが上がる原因となります。具体的な例としては、送り速度を材質の状態や工具の種類に応じて微調整し、試作品加工による仕上がりの確認を行うことです。このような適切な送り速度の設定により、MCナイロン加工時の品質保持と生産効率の向上が期待できます。
刃先の温度管理
刃先の温度管理の重要性
要素 | 説明 |
---|---|
MCナイロンの特性 | 摩擦熱によって物性が変化しやすく、精度が低下する |
刃先温度の管理 | 切削精度を維持し、工具の摩耗を防ぐために重要 |
推奨される切削条件
条件 | 説明 |
---|---|
切削速度 | 低速での切削が推奨される |
冷却液の使用 | 摩擦熱を取り除くために冷却液を積極的に使用する |
回転数 | ゆったりとした速度で加工を行う |
刃先温度管理のポイント
- 低速切削: 高速切削は摩擦熱を増加させるため、低速での加工が推奨されます。
- 冷却液の使用: 冷却液は摩擦熱を効率的に取り除き、加工面の品質を保ちます。
- 回転数の調整: 回転数を抑えることで、刃先の温度を管理し、工具の摩耗を防ぐことができます。
適切な切削速度と冷却液の使用、回転数の調整により、MCナイロンの加工品質を高め、経済的な運用が実現できます。刃先の温度管理は、MCナイロン加工において最適な切削条件の一部として重要です。
MCナイロン青色の推奨加工条件
青色MCナイロンとは
工作機械でMCナイロンを加工する際の最適な切削条件を見極めることは、製品の品質向上と加工効率の向上に欠かせない要素です。MCナイロンは、摩擦係数が低く、耐摩耗性に優れており、工業部品などに広く用いられている素材です。しかし、切削条件が適切でないと、加工面が荒れたり、寸法が不正確になる可能性があります。具体的には、工具の刃先温度や切削速度、送り速度、そして切削液の使用が重要なポイントとなります。例えば、切削速度を適切に設定することで、MCナイロン固有の熱膨張を防ぎ、精度の高い加工を実現することが可能です。また、適正な切削液の使用は、切削熱の発生を抑え、摩耗を減らす効果があります。したがって、これらの切削条件を適正に管理することが、MCナイロンの加工における成功の鍵です。最適な切削条件の下で加工を行うことが、品質と効率の両立を実現するために必要不可欠です。
青色MCナイロンの特性と加工の注意点
青色MCナイロンの特性
特性 | 説明 |
---|---|
耐摩耗性 | 摩耗に強く、長期間使用できる |
強度 | 高い強度を持ち、多様な工業部品に利用される |
加工の注意点
加工方法 | 推奨される条件 |
---|---|
切削速度 | 低めに設定して熱による軟化を防ぐ |
切削工具 | 硬度の高い材料で鋭い刃を維持する |
ドリル加工 | 回転数を落とし、切削液を十分に使用する |
フライス加工 | カッターの歯数を多くして切削負担を分散させる |
加工条件の管理
- 切削速度: MCナイロンの熱による軟化を防ぐため、切削速度を低めに設定します。
- 切削工具: 鋼よりも硬度の高い材料を選び、刃を鋭く保つことで、精密な加工が可能になります。
- ドリル加工: 回転数を抑え、切削液で摩擦熱を管理することが推奨されます。
- フライス加工: 多くの刃数で切削負担を分散させることで、効率的な加工が実現します。
これらの条件を適切に管理することで、青色MCナイロンの加工効率と品質を高めることができ、製品の特性を最大限に活かすことができます。
青色MCナイロン専用の切削条件
切削条件のポイント
条件 | 推奨値 |
---|---|
切削速度 | 低~中速での切削が推奨される |
送り速度 | 適切な速度で均等な加工を行う |
切削工具の材質 | 熱がこもりにくく、摩擦を低減する材質が最適 |
冷却液の使用 | 適正な量で摩擦熱を管理する |
工具の管理
管理項目 | 推奨対応 |
---|---|
工具の点検 | 定期的な点検を行い、摩耗をチェックする |
工具の交換 | 摩耗が進んだ場合は早めに交換する |
切削条件の最適化
- 切削速度と送り速度: 低~中速で切削し、均等な送り速度を保つことで、加工精度を向上させます。
- 切削工具の材質: 熱がこもりにくく、MCナイロンとの摩擦を低減する材質の工具を選ぶことが重要です。
- 冷却液の使用: 適正量の冷却液を使用することで、摩擦熱を効果的に管理し、加工品質を保ちます。
- 工具の管理: 定期的な点検と必要に応じた交換で、工具の性能を維持し、精密な加工を継続できます。
これらの条件を整えることで、青色MCナイロンの加工効率と品質を高め、生産性の向上に寄与します。
MCナイロン外径切削のための工具選択
外径切削工具の種類
MCナイロンの加工において、外径切削工具の選定は重要です。MCナイロンは耐摩耗性が高く、自己潤滑性を持つものの、熱に弱く変形しやすいため、適切な工具選びと切削条件が必要です。以下は、MCナイロンの外径切削における主要な工具とその特性です。
切削工具の種類と特性
工具の種類 | 特徴 | 使用例 |
---|---|---|
カーバイド工具 | 高硬度で摩耗に強い、熱による劣化が少ない | 外径加工、精密部品の加工 |
HSS工具 | コストが比較的低いが、耐熱性は劣る | 経済的な加工が必要な場合 |
ダイヤモンド工具 | 非常に高い耐摩耗性、長寿命 | 高精度加工や高硬度材料の切削 |
CBN工具 | 高耐摩耗性、熱安定性が良い | 高速切削や硬度の高い材料に適している |
切削条件の最適化
条件 | 推奨値 |
---|---|
切削速度 | 低~中速での設定が推奨 |
送り速度 | 適切に調整、過度に速い速度は避ける |
切削深さ | 少なめに設定し、一度に大量の材料を削らない |
工具選定と条件設定のポイント
- 工具の選定: MCナイロンの特性を考慮し、摩耗に強く熱に耐性のある工具を選ぶことが重要です。カーバイド工具やダイヤモンド工具は高精度加工に適しています。
- 切削条件の調整: 切削速度を低~中速に設定し、送り速度は慎重に調整します。切削深さは控えめに設定し、一度に多くの材料を削らないようにします。
これらの工具と切削条件を適切に選定・設定することで、MCナイロンの特性を最大限に活かした加工が可能になります。加工品質の向上と工具の耐用年数の延長に寄与します。
MCナイロン加工に適した工具の特徴
MCナイロンの加工には、特有の切削条件と工具が求められます。MCナイロンは優れた耐摩耗性と機械的強度を持つ一方で、熱に弱く変形しやすいため、適切な工具と条件設定が必要です。以下は、MCナイロン加工に適した工具の特徴です。
工具の種類と特徴
工具の種類 | 特徴 | 利点 |
---|---|---|
カーバイド工具 | 高硬度で耐摩耗性に優れ、熱にも強い | 精密加工が可能、工具寿命が長い |
HSS工具 | コストが低く、熱伝導性が高い | 経済的、柔軟な加工が可能 |
ダイヤモンド工具 | 非常に高い耐摩耗性と長寿命 | 高精度加工、高硬度材料に対応 |
CBN工具 | 高い耐摩耗性と熱安定性 | 高速切削や硬度の高い材料に適する |
切削条件の最適化
条件 | 推奨値 |
---|---|
切削速度 | 低~中速での設定が推奨 |
送り速度 | 適切に調整し、過度に速い速度は避ける |
切削深さ | 少なめに設定し、一度に大量の材料を削らない |
工具選定と条件設定のポイント
- 工具の選定: MCナイロンの加工には、シャープで硬質な工具が最適です。カーバイド工具やダイヤモンド工具が推奨されます。
- 切削条件の調整: 切削速度は低~中速で維持し、送り速度を適切に調整します。切削深さは控えめに設定し、一度に多くの材料を削らないようにします。
これらの特徴を持つ工具を選び、適切な切削条件を設定することで、MCナイロンの加工精度と効率を向上させることができます。最終的には、品質を保ちつつ生産効率を高めるために、これらの条件の最適化が重要です。
最適な工具選択のためのポイント
MCナイロンを工作機械で加工する際の最適な工具選択と切削条件は、加工品質と効率を大きく左右します。以下に、工具選定の際の重要なポイントと推奨される条件について整理します。
工具選定のポイント
ポイント | 詳細説明 |
---|---|
工具の材質 | カーバイド工具やダイヤモンド工具が推奨される。高硬度で耐摩耗性が高く、MCナイロンの加工に適している。 |
工具の形状 | シャープで精密な刃先を持つ工具を選定することで、加工精度を高める。特に、フラットエンドミルやドリルが有効。 |
切削速度 | MCナイロンの熱変形を防ぐため、低めに設定することが重要。一般的には100~300m/minが推奨される。 |
送り速度 | 高すぎる送り速度はMCナイロンの割れを引き起こす可能性があるため、適切な速度(0.05~0.2mm/rev)を設定する。 |
切削液の使用 | 冷却と潤滑のために切削液を使用することで、摩擦熱を抑制し、加工精度の向上と工具寿命の延長が期待できる。 |
切削条件の最適化
条件 | 推奨値 |
---|---|
切削速度 | 100~300m/min |
送り速度 | 0.05~0.2mm/rev |
切削深さ | 少なめに設定し、一度に大量の材料を削らない |
工具と条件選定の重要性
- 工具選定: MCナイロンの加工には、耐摩耗性と硬度の高い工具が必要です。カーバイドやダイヤモンド工具はその特性に適しています。
- 切削条件の設定: 切削速度や送り速度を適切に設定することで、加工時の熱変形や割れを防ぎ、高品質な仕上がりを実現します。
- 切削液の使用: 切削液を使用することで、熱の発生を抑え、工具の寿命を延ばすと共に、加工精度を向上させることができます。
これらのポイントを考慮して工具を選定し、切削条件を最適化することで、MCナイロンの加工効率と品質が大幅に向上します。最適な条件設定が、加工精度の向上と生産性の向上につながります。
MCナイロンのエンドミル加工とバリ問題
エンドミル加工の概要
MCナイロンの加工に際して最適な切削条件を見極めることは、加工品質の向上と工具寿命の延長に不可欠です。MCナイロンは、その高い耐摩耗性と自己潤滑性から多くの工業分野で重宝されますが、加工時の熱による変形や割れが生じやすいため、適切な切削条件の設定が求められます。
具体的には、低い切削速度での加工が推奨されます。これにより、発熱を抑制し、MCナイロンの物性変化を防ぎます。また、切削時には冷却液の使用が効果的であり、工具と材料の摩擦熱を低減し、製品の精度を保持することができます。さらに、シャープな刃物を用いて、連続的な切削を行うことが重要です。摩耗した刃物では精度の高い加工が困難となります。
以上の条件を遵守することで、MCナイロンの加工時の問題を最小限に抑え、製品の品質を高めることが可能になります。理想的な切削条件で加工を行うことは、コスト削減にも繋がり、生産性の向上に寄与するでしょう。
MCナイロン加工時のバリの原因
MCナイロンを加工する際にバリが発生する原因は、様々な切削条件や管理の不足に起因します。バリは製品の品質に悪影響を及ぼし、追加の手間がかかるため、これを最小限に抑えるための対策が重要です。以下に、MCナイロン加工時のバリの主な原因とそれに対する対策を示します。
バリの原因と対策
原因 | 詳細説明 | 対策 |
---|---|---|
切削速度が速すぎる | 高速切削による熱の発生がバリを生む。材料が溶けてしまい、バリができやすくなる。 | 適正な切削速度(一般的には100〜300m/min)を選定し、発熱を抑える。 |
切削速度が遅すぎる | 切削が遅すぎると、工具の摩耗が激しくなり、加工が不安定になることでバリが発生する。 | 適切な速度で加工を行い、工具の摩耗を防ぐ。 |
切りくずの排出不良 | 切りくずが排出されず、加工面に残るとバリの原因になる。 | 切りくずの排出をスムーズにするために適切な切削液を使用する。 |
刃先の冷却不足 | 冷却が不十分だと、過度な熱が発生し、バリが発生する。 | 適切な冷却液を使用し、刃先の温度管理を行う。 |
工具の摩耗 | 摩耗した工具は切削精度が低下し、バリが発生する。 | 定期的に工具の点検と交換を行い、常に鋭い刃を保つ。 |
バリ発生を防ぐための加工条件
条件 | 推奨値 |
---|---|
切削速度 | 100〜300m/min |
送り速度 | MCナイロンの硬さに応じて調整(0.05~0.2mm/revが一般的) |
切削液の使用 | 冷却と潤滑のために適切な切削液を使用する |
刃先の冷却 | 適切な冷却液の使用と冷却条件の設定 |
まとめ
MCナイロン加工におけるバリの発生は、切削条件や刃先の冷却管理に大きく依存します。適切な切削速度と送り速度の設定、冷却液の使用、そして工具のメンテナンスが、バリの発生を抑えるための鍵です。これらの条件を適切に設定することで、製品の品質向上と生産効率の両立が可能になります。
切削条件の重要性
切削加工において、切削条件は素材の品質と加工効率に大きく影響を与えます。MCナイロンなどの樹脂素材は特に適切な切削条件を守ることが重要で、適切に設定された条件は部品の精度を高め、加工の安定性や効率性を向上させます。以下に切削条件の重要性について説明します。
切削条件の要素
要素 | 重要性 |
---|---|
切削速度 | 切削速度が速すぎると熱が発生し、材料が変形したり、摩耗が増加する可能性があるため、適切な速度設定が必要。 |
送り速度 | 送り速度が速すぎると切削面が粗くなるため、精度を確保するために適切な送り速度が重要。 |
切削深さ | 大きな切削深さは工具の摩耗を促進するため、深さは適度に保つべき。 |
冷却方法 | 樹脂材料は熱に敏感なため、適切な冷却を行うことで加工温度を管理し、熱膨張や変形を防ぐ。 |
工具選定 | 樹脂材料に適した工具を選ぶことで、切削効率や仕上がりが向上し、工具の寿命も延ばせる。 |
切削条件の影響
- 熱影響: 樹脂は熱に敏感で、過剰な切削熱は材料の特性を変化させ、寸法精度や表面品質に影響を与えます。切削速度や送り速度を適切に設定することは熱影響を最小限に抑えるために重要です。
- 切削面の仕上がり: 不適切な切削条件は、切削面に荒れやバリを引き起こす原因となり、仕上げの品質が低下します。送り速度や切削深さを適切に調整することで、滑らかな表面を得ることができます。
- 工具寿命: 切削条件が悪いと、工具の摩耗が早くなり、頻繁に工具交換が必要になります。適切な切削条件を設定することで、工具寿命を延ばし、コストを削減することができます。
切削条件はMCナイロンを含む樹脂素材の加工において、加工精度や効率、品質に直接的な影響を与えます。適切な条件設定を行うことで、加工中のトラブルを防ぎ、良好な仕上がりと長期的な運用コスト削減が可能になります。特に樹脂素材では、熱や切削力に敏感であるため、細かい調整が求められます。
バリ除去のためのアフターケア
工作機械でMCナイロンを加工する際には、最適な切削条件が非常に重要です。なぜならば、MCナイロンは摩擦熱によって軟化しやすい性質を持っており、切削条件が適切でないと加工精度に大きく影響するからです。具体的な条件としては、切削速度、送り速度、削り取る厚み(切削深さ)、使用する刃物の材質や形状などが挙げられます。例えば、切削速度を速くしすぎるとMCナイロンが熱で溶け、逆に遅すぎるとバリが発生しやすくなります。また、適切な刃物を選択することも重要で、MCナイロン加工用に特化したものや、刃先のコーティングなどが施されている工具を選ぶと良いでしょう。これらの条件を最適化することで、精度高く、かつ効率的なMCナイロンの加工が可能となります。したがって、最適な切削条件の選定は、MCナイロンを使用した製品の品質保持に不可欠であると言えるでしょう。
実践!MCナイロンの加工ポイント
切削条件の事前検討
工作機械でMCナイロンを加工する際の最適な切削条件については、材質の特性を考慮することが重要です。MCナイロンは熱に弱く、切削時には熱が発生しやすいため、低い切削速度を選択することが望ましいです。さらに、鋭利な切削工具を用いて、精密な仕上がりを目指すべきです。実例としては、刃の摩耗を防ぎながらスムーズな切削を行うために、冷却液を使用することが効果的です。このように適切な切削条件を設定することで、MCナイロンの加工品質を向上させ、製品の信頼性を高めることができます。最後に、これらの条件を適用することで、長期にわたる機械の性能維持にも貢献します。
加工誤差を防ぐための工夫
工作機械でMCナイロンを加工する時、最適な切削条件を選定することは、加工精度を高め、製品の品質を確保するうえで重要です。MCナイロンはその優れた機械的特性から、さまざまな工業用部品に使用されていますが、切削加工には特有の注意が必要です。理想的な切削条件とは、刃の速度、送り速度、切削深さを含みますが、MCナイロンの場合は特に、過熱を防ぐための冷却方法にも気を配る必要があります。
例えば、刃の速度はMCナイロンの熱可塑性を考慮して、適度に抑えることが推奨されます。また、精密な加工を要する際は、送り速度を下げ、切削深さを浅くすることで、加工誤差を防ぎながら滑らかな表面を得ることが可能です。さらに、連続切削を行う場合には、断続的に冷却液を噴射することで、MCナイロンが過熱して軟化するのを防ぎます。
以上のように、MCナイロンを加工する際は、材料の特性に合わせた切削条件の選定が不可欠です。適切な切削条件で加工を行うことで、加工誤差を最小限に抑え、品質の高い製品を製造することができるでしょう。
効率的な加工プロセスの設計
工作機械を用いてMCナイロンを加工する際、最適な切削条件を見極めることが重要です。MCナイロンはその耐摩耗性や耐薬品性に優れるため、工業分野で広く利用されていますが、適切な切削条件が設定されていないと加工時に品質が低下する恐れがあります。具体的には、切削スピードや送り速度、切削液の使い方がポイントです。例えば、切削速度を高くしすぎるとMCナイロンが溶け出すことがありますし、逆に低すぎると切りくずの排出が悪くなります。適正な送り速度を保つことで精度の高い加工が可能になり、切削液を適切に使うことで熱の発生を抑え、刃の摩耗を防ぐことができます。各工作機械や加工するMCナイロンの特性によって最適な条件は異なりますが、これらの基本を理解し、適応させることが必要です。最後に、これらの条件を適切に管理することで、効率的かつ高品質なMCナイロンの加工が可能となります。
MCナイロン加工時のトラブルシューティング
加工中のトラブルとその対処法
MCナイロンを工作機械で加工する際には、さまざまなトラブルが発生する可能性があります。これらのトラブルを未然に防ぐためには、適切な切削条件の設定とトラブル発生時の対処法を理解することが重要です。以下に、一般的な加工中のトラブルとその対処法を示します。
トラブルとその原因
トラブル | 原因 | 対処法 |
---|---|---|
切削面の粗さ | 刃の速度が適切でない、送り速度が不適切 | 刃の速度と送り速度を見直し、適切に設定する。 |
刃物の破損 | 送り速度が速すぎる、切り込み深さが深すぎる | 送り速度と切り込み深さを適切に設定し直す。 |
材料の溶け | 刃の速度が速すぎる、冷却が不十分 | 刃の速度を低く設定し、冷却液を適切に使用する。 |
加工時間のロス | 送り速度が遅すぎる、切り込み深さが浅すぎる | 送り速度と切り込み深さを調整し、加工効率を上げる。 |
工具の過度な摩耗 | 刃の速度が高すぎる、切り込み深さが不適切 | 刃の速度と切り込み深さを適切に設定し、工具を定期的に交換する。 |
トラブル発生時の対処法
トラブル | 対処法 |
---|---|
切削面の粗さ | 刃の速度や送り速度を再確認し、調整する。加工面の状態を確認する。 |
刃物の破損 | 刃物の状態をチェックし、必要に応じて交換する。加工条件を見直す。 |
材料の溶け | 刃の速度を下げ、冷却液の使用を増やす。冷却状態を確認する。 |
加工時間のロス | 送り速度を上げ、切り込み深さを適切に調整する。効率的な加工条件を再設定する。 |
工具の過度な摩耗 | 工具の定期点検と交換を行い、切削条件を見直す。工具寿命を延ばすための管理を徹底する。 |
まとめ
MCナイロン加工中に発生するトラブルは、切削条件の設定や管理により予防または対処が可能です。適切な切削速度、送り速度、切り込み深さの設定と、冷却液の適切な使用がトラブルの発生を抑えるカギとなります。トラブルが発生した際には、原因を特定し、適切な対策を講じることで、加工品質の向上と効率化が図れます。
切削条件の調整と最適化
MCナイロンを工作機械で加工する際、切削条件の調整と最適化は加工品質と工具寿命を確保するために非常に重要です。以下に、最適な切削条件の調整とその具体的なポイントを示します。
切削条件の調整ポイント
切削条件 | 調整ポイント | 具体例 |
---|---|---|
切削速度 | MCナイロンは高い切削速度で溶着する恐れがあるため、切削速度は低く設定することが推奨される。 | 切削速度を100~300m/minに設定し、加工中の発熱を抑える。 |
送り速度 | 適度な送り速度を設定することで、粗削りと仕上げ削りのバランスを取る。高すぎると表面粗さが増す。 | 送り速度を0.05~0.2mm/revに設定し、均一な仕上げを実現する。 |
切り込み量 | 切り込み量が多すぎると工具に負担がかかるため、少なめに設定する。 | 切り込み深さを調整し、材料を少しずつ削ることで効率的な加工を行う。 |
冷却液 | 冷却液の使用は摩擦熱を抑えるために重要であり、十分な量を使用する。 | 適切な冷却液を使用し、加工中の発熱を抑えることで精度を保つ。 |
最適化のプロセスと例
- 初期設定と試行:
- 初期の切削条件を設定し、試し削りを行う。
- 例: 切削速度を150m/min、送り速度を0.1mm/revに設定して試行する。
- データ収集と分析:
- 加工結果を分析し、加工面の状態や工具の摩耗具合を確認する。
- 例: 切削面の粗さや工具の摩耗度合いを測定する。
- 条件の調整:
- 収集したデータをもとに切削条件を調整する。
- 例: 切削速度を200m/minに、送り速度を0.15mm/revに変更して再試行する。
- 最適条件の確立:
- 最適な条件を見つけ出し、実際の生産に適用する。
- 例: 切削速度を180m/min、送り速度を0.12mm/revに設定し、最良の結果を得る。
まとめ
MCナイロンの切削加工においては、切削速度、送り速度、切り込み量、冷却液の使用などの条件を適切に調整し、最適化することで、加工品質を向上させることができます。これにより、精密かつ効率的な加工が実現し、最終的には生産コストの削減にも繋がります。条件の最適化は試行錯誤を伴うプロセスですが、適切な管理により高品質な製品の生産が可能になります。
定期的なメンテナンスの重要性
MCナイロンの加工において最適な切削条件を見極めることは、製品の品質を保ちつつ効率的に作業を進めるために非常に重要です。MCナイロンは、その優れた耐摩耗性や耐衝撃性から多くの産業分野で利用されていますが、適切な切削条件を用いないと加工時に発生する熱により材料が変形したり、表面が荒れたりすることがあります。具体的な例としては、カッターの速度や送り速度、切削液の使用が挙げられます。これらを適切に設定することで、MCナイロンを滑らかに切削し、精度の高い加工を実現できます。最終的には、繰り返しのテストカットを行いながら、材質や形状に最適な切削条件を見つけ出すことが求められます。品質を確保しつつ効率的な生産を目指すためには、最適な切削条件の選定が欠かせません。
結論
MCナイロン加工の成功のためのキーポイント
MCナイロンを工作機械で加工する際に最適な切削条件を知ることは、加工の品質と効率を大きく向上させるために不可欠です。適切な切削条件には、切削速度、送り速度、切り込み量が含まれますが、この中でもMCナイロンの場合、切削速度が特に重要とされています。MCナイロンは熱に弱く、高速での加工によって生じる熱が材料の変質や融解を引き起こす原因となるため、適度な切削速度の選定が求められます。例えば、一般的なMCナイロンの場合、切削速度を200〜300m/min程度に設定することが推奨されています。また、シャープな刃物を使用し、定期的な刃物の交換を行うことで、精度の高い加工が可能になります。これらの条件を適切に管理することで、MCナイロンの加工時に発生する問題を避け、製品の品質を保つことができます。
継続的な学習と技術の向上
工作機械を用いたMCナイロンの加工において、最適な切削条件を知ることは、品質向上と効率化の鍵です。MCナイロンは熱や摩耗に強い素材として知られており、精密な加工が求められる部品製造において重要な役割を担っています。最適な切削条件とは、具体的には切削速度、送り速度、切削深さが均衡をもち、材料の特性に最も適した状態を指します。例えば、MCナイロンの場合、熱による変形や加工時の精度を保つためには低めの切削速度を選択するのが一般的です。また、工具の摩耗を抑制し、仕上がりの表面粗さを最適に保つためには、切削深さや送り速度にも注意が必要です。これらの条件を適切に設定することで、MCナイロンはその優れた特性を存分に発揮し、耐久性や精度が高い部品へと加工されます。結論として、MCナイロンの加工における切削条件は、材料の性質を熟知し、それに合わせた設定を施すことが不可欠であり、これにより高品質な製品製造にとって重要な要素となるのです。
まとめ
MCナイロンを工作機械で加工する際には、適切な切削条件が重要です。切削速度や刃先形状、切削油の使用などを適切に設定することで、加工精度や工具寿命を向上させることができます。また、適切な切削条件によって切屑の排出や加工表面の仕上がりにも影響があります。MCナイロンの特性を考慮し、適切な切削条件を設定することが加工品質向上のポイントです。