MCナイロンの絶縁特性とは?エンジニア必見の解説
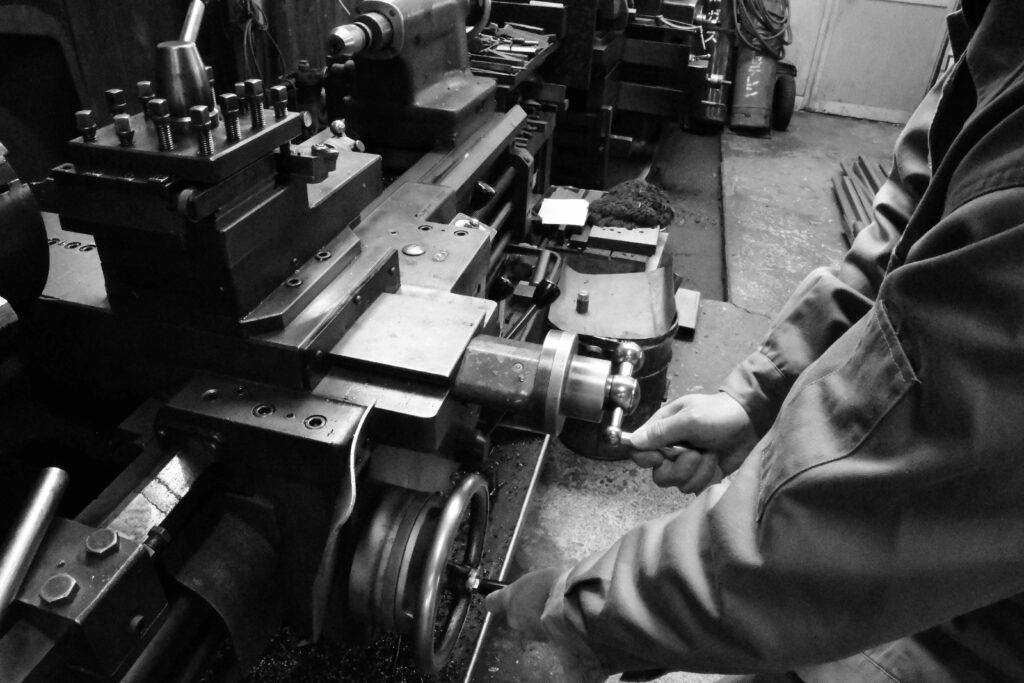
MCナイロンという素材は、エンジニアや製造業界にとって重要な役割を果たしています。特に、その絶縁特性は注目に値します。MCナイロンの絶縁特性とは一体何なのでしょうか?本記事では、その疑問にお答えするために、MCナイロンの絶縁特性について詳しく解説いたします。エンジニアの方々にとって必見の内容となっておりますので、ぜひ最後までご覧ください。MCナイロンがどのように素晴らしい絶縁性を持つのか、そのメカニズムや利点について解説いたします。是非、MCナイロンの素晴らしい特性についてご一緒に探求していきましょう。
MCナイロンとは?
MCナイロンの概要
MCナイロン(モノマーキャストナイロン、Monomer Casting Nylon)は、ナイロン6(ポリアミド6)の一種で、モノマー状態のカプロラクタムを鋳型内で重合させて成形する方法で製造される高機能エンジニアリングプラスチックです。従来の押出成形ナイロンと比較して、分子量が高く、機械的強度・耐摩耗性・耐熱性・寸法安定性に優れているのが特徴です。
MCナイロンは大型部品の一体成形が可能で、機械加工性も高いため、歯車、ベアリング、スプロケット、ガイドレールなど、摩擦や衝撃に耐える必要がある産業用部品に広く使用されています。特に金属に代替される軽量部材として注目されており、加工後の仕上がり精度にも優れています。
MCナイロンの歴史と発展
MCナイロンの開発は、1950年代にドイツをはじめとしたヨーロッパ諸国でスタートしました。従来のナイロン樹脂は、主に射出成形や押出成形で製造されていたため、大型部品や複雑形状の成形には制限がありました。これを解決するために開発されたのが、カプロラクタムを直接重合させる「鋳込み法(キャスト法)」です。
日本では、1970年代以降に工業用途での需要が高まり、各プラスチックメーカーが相次いでMCナイロンの製造・加工技術を確立。以降、産業機械、自動車、食品製造装置、建設機械など、幅広い分野で使用が進み、現在では高性能プラスチック材料として確固たる地位を築いています。
現在では、ベーシックなMCナイロンに加え、各種添加剤を加えたグレード(耐熱タイプ、帯電防止タイプ、潤滑剤添加タイプなど)も開発されており、用途に応じて使い分けられています。
MCナイロンの絶縁性
絶縁特性の基礎知識
絶縁性とは、電気が通りにくい性質を指し、電気部品や電子機器においては、漏電や短絡を防ぐために重要な特性です。絶縁性の指標には「体積抵抗率」や「絶縁破壊強度」などがあり、数値が高いほど電気を通しにくい材料とされます。プラスチック材料は一般的に高い絶縁性を持ち、MCナイロンもその代表的な素材の一つです。
MCナイロンの絶縁性能
MCナイロンは、ポリアミド系樹脂でありながら、非常に優れた電気絶縁性を有しています。特に体積抵抗率は10¹³〜10¹⁵Ω・cmと高く、常温・乾燥状態での絶縁性能は非常に安定しています。また、絶縁破壊強度も高いため、薄肉でもしっかりと絶縁効果を維持できます。
ただし、ナイロン系樹脂は吸湿性があるため、長期間にわたり高湿度下に置かれると、絶縁性能がやや低下する傾向があります。そのため、高湿環境での使用には、吸湿対策(防湿処理や適切な形状設計)が必要です。
MCナイロンの電気的利用事例
MCナイロンは、その優れた絶縁性と機械的強度を活かし、以下のような電気・電子関連分野で利用されています。
- 変圧器やモーターの絶縁スペーサー
- 制御盤内の絶縁プレート
- 高電圧部品の絶縁ブロック
- プラグ・コネクターまわりの絶縁部品
- ロボットや自動機の電装部品用ベース
これらの部品では、電気的な安全性を確保しながら、耐衝撃性や耐摩耗性といった機械特性も求められるため、MCナイロンの特性が非常にマッチします。特に、軽量化と絶縁を両立したい設計では、金属からの代替材としても選ばれることが多くなっています。
MCナイロンの物理的・化学的特性
材料性質の概
MCナイロン(モノマーキャストナイロン)は、ナイロン6を基にしたエンジニアリングプラスチックの一種で、モノマーを鋳造しながら重合させて成形されるため、通常の押出し成形ナイロンに比べて高い結晶性と均一な分子構造を持ちます。これにより、優れた機械的・熱的・化学的性質を併せ持つ材料として、多くの産業分野で使用されています。
機械的特性
- 引張強さ:70〜90 MPa
- 曲げ強さ:100〜130 MPa
- 衝撃強さ(ノッチ付き):4〜7 kJ/m²
- 硬度(ロックウェル R):100〜120
- 摩耗抵抗性:優れており、ベアリングやスライドガイドに使用可能
MCナイロンは耐摩耗性に特に優れており、摺動部材(滑り部品)としての適性が高く、自己潤滑性にも富んでいます。
熱的特性
- 耐熱温度(連続使用):100〜120℃
- 熱変形温度(1.8MPa):170〜180℃
- 融点:約220℃
- 熱伝導率:約0.25 W/m·K
耐熱性は高く、120℃前後までの環境であれば長時間使用可能です。ただし、高温下では機械強度が徐々に低下していくため、設計上の配慮が必要です。
化学的耐性
- 耐薬品性:アルカリ、油類、弱酸には良好な耐性
- 耐水性:比較的高いが吸湿性があるため寸法変化に注意
- 耐溶剤性:一般的な有機溶剤にはやや弱い
- 耐酸性:強酸に対しては劣化するため注意が必要
MCナイロンは油やアルカリ溶液への耐性が高いため、潤滑油や切削油を使用する環境でも安定した性能を発揮します。一方で、水分を吸収しやすいため、寸法精度が求められる場面では乾燥処理や設計補正が必要です。
MCナイロンとPOMの比較
それぞれの材料の特徴
- MCナイロン(モノマーキャストナイロン)
- 高い引張強度と耐摩耗性
- 優れた自己潤滑性
- 高い衝撃吸収性と柔軟性
- 吸湿性があるため寸法変化に注意
- 大型・厚物部品の成形に適している
- POM(ポリアセタール/アセタール樹脂)
- 極めて高い寸法安定性
- 優れた耐摩耗性と滑り性
- 吸湿性が非常に少なく湿度の影響を受けにくい
- 高剛性・高強度で機械加工性に優れる
- 化学薬品への耐性はアルカリにやや弱いが酸には比較的安定
適切な使用環境の選定
- MCナイロンが適する環境
- 衝撃が多い箇所(ベアリング、ギア、スライドプレート)
- 高負荷・中速の摺動部品
- 潤滑油が多用される環境
- 大型部品を一体成形したい場合
- POMが適する環境
- 高精度な寸法管理が求められる場面(歯車、カム、ガイド部品など)
- 乾燥環境・水分が少ない環境
- 高速回転する摺動部品
- 加工精度と剛性が重要視される用途
用途に応じた材料選択
- 選定ポイント:
- 寸法精度や湿度による寸法変化がNG → POM
- 耐衝撃性や柔軟性が求められる → MCナイロン
- 自己潤滑性を重視する摺動部品 → 両者とも適するが、環境により選定
- 大型・厚物部品を低コストで製造したい → MCナイロンが有利
- 高速回転・高精度部品 → POMが優位
MCナイロンとPOMは似た性質を持ちながらも、吸湿性や剛性、加工精度に違いがあるため、使用環境や目的に応じて最適な選定が求められます。
MCナイロンの適用と利用分野
一般的な用途
- ギア、スプロケット、ベアリング、スライドプレートなどの摺動部品
- ローラー、ブッシュ、スペーサーなどの衝撃吸収を必要とする部品
- パッキン、シール、ガイドなどの絶縁・耐摩耗部品
- 搬送ライン用部材、食品機械の部品など
MCナイロンは優れた耐摩耗性と自己潤滑性を持ち、金属部品の代替材料として広く使用されています。
エンジニアリングプラスチックとしての役割
- 軽量化と省エネルギー化
金属の代わりに使用することで機械全体の軽量化が図れ、動力消費を削減できます。 - 静音化とメンテナンス性の向上
衝撃吸収性や自己潤滑性によって騒音を低減し、潤滑剤不要で保守も容易になります。 - 耐摩耗・耐腐食性の確保
環境条件の厳しい場所でも長寿命を実現し、部品交換の頻度を低減できます。
産業別利用事例
- 機械・産業機器分野
- 搬送ラインのローラー・ガイド部品
- 各種工作機械の摺動部・補助機構パーツ
- 食品加工機械
- 衛生的で潤滑不要な摺動部品
- 耐薬品性が求められる洗浄対応部品
- 自動車・輸送機器
- 車体組立ラインの治具・カバー類
- フォークリフトなどの可動部品
- 電子・電機産業
- 絶縁体としてのガイド、スペーサー
- EMIノイズ対策を兼ねた構造部材
- 建設・土木機械
- 建機のアームや可動部のすべり材
- クレーンのガイドや保護材
MCナイロンは「軽くて強い」「すべりが良い」「腐食しにくい」という特性から、あらゆる産業で金属の代替として活躍しています。
エンジニアリングプラスチックの選定方法
材料選定の基準
- 使用環境
温度、湿度、薬品、屋外か屋内かなど、設置条件に対応した材料選定が必要です。 - 機械的要件
引張強度や圧縮強度、耐摩耗性、衝撃吸収性などが重視される場面で材料特性を評価します。 - 電気的要件
絶縁性や導電性など、電気的な安全性・機能が求められる用途での適合確認が必要です。 - コストと加工性
材料費、加工のしやすさ、量産性などから、トータルコストで最適な材料を選定します。 - 法規制・安全性
食品接触適合(FDA、食品衛生法)や環境規制(RoHS、REACH)を満たす必要があります。
MCナイロンを選ぶ理由
- 高い耐摩耗性と機械的強度により、摺動部品や構造体に向いています。
- 自己潤滑性があり、無給油運転が可能で、メンテナンス頻度を低減できます。
- 衝撃吸収性が高く、可動機構の緩衝材としても効果を発揮します。
- 化学的に安定し、酸・アルカリなどに対する耐性もあり、厳しい環境でも使用可能です。
- 切削加工性が良く、複雑形状の部品や短納期対応に適しています。
他材料との比較検討
- POM(ジュラコン)
寸法安定性と低摩擦性があり、精密機械部品やギアに使用されます。耐薬品性も高いですが、吸水性がややあり、乾燥環境での使用が推奨されます。 - PEEK
高温下でも強度・剛性が維持され、耐薬品性も高いため、航空・医療分野など高機能用途に適しています。ただしコストは高めです。 - PTFE(テフロン)
最高レベルの耐薬品性と非粘着性、低摩擦特性を持ち、シールやガスケット、ライニングに最適ですが、機械的強度はやや劣ります。 - ポリカーボネート
耐衝撃性に優れ、透明性も高いため、保護カバーや照明用途でよく使われます。耐薬品性や耐摩耗性は他材料に劣ります。
それぞれの材料には長所と短所があるため、使用条件と求められる性能を照らし合わせた上で、最適な素材を選定することが重要です。
MCナイロンの加工技術
加工方法の種類と特徴
- 切削加工
一般的な旋盤、フライス盤、マシニングセンターを用いて行います。MCナイロンは機械加工性に優れ、寸法精度が求められる部品にも適しています。バリが出にくく、表面も比較的綺麗に仕上がります。 - 穴あけ加工(ドリリング)
樹脂用の刃物や切削条件を選定することで、熱変形や割れを防ぎつつ加工が可能です。深穴加工の際はチップ排出や熱対策を考慮する必要があります。 - 切断加工
バンドソーや丸鋸を用いた切断が多く、低速での切断が推奨されます。熱を持ちやすいため、切断面の変形や溶けを防ぐため冷却を併用する場合もあります。 - 接着加工(非推奨)
MCナイロンは表面の化学的安定性が高いため、一般的な接着剤では接合が難しく、機械的な固定やネジ止めが主に用いられます。 - 溶接(溶着)加工
ナイロン同士であれば熱風溶着や超音波溶着が可能な場合もありますが、MCナイロンは結晶性が高いため溶着には適しません。基本的には一体加工か機械的接合が前提です。
加工時の注意点
- 熱変形への配慮
加工中に発生する摩擦熱によりMCナイロンが軟化・変形する恐れがあります。冷却手段(エアブロー、冷却液)を適切に取り入れましょう。 - 吸水性の管理
MCナイロンは吸水性があるため、湿度や保管環境によって寸法変化が生じることがあります。寸法精度が厳しい場合は、加工前後の乾燥や寸法補正を考慮する必要があります。 - 工具の選定
切れ味の良い超硬工具や樹脂専用工具の使用が望ましいです。摩耗した工具ではバリの発生や加工面の粗さが増し、寸法精度にも影響します。 - クランプ方法
柔らかく変形しやすい素材のため、強いクランプは歪みの原因になります。広い面で圧力を分散させる治具やゴムパッドなどの併用が効果的です。
MCナイロンの特性を理解したうえで、適切な加工方法と管理を行うことで、高精度な成形部品や摺動部品を安定して製作することが可能になります。
MCナイロンのメンテナンスと耐久性
長期使用における耐久性
MCナイロンはエンジニアリングプラスチックの中でも高い機械的強度と耐摩耗性を持ち、長期使用において優れた耐久性を発揮します。特に以下の特性が寿命を延ばす要因となっています:
- 耐摩耗性:連続摺動や繰り返しの機械動作でも摩耗が少なく、形状を長期間保持。
- 自己潤滑性:摺動部での潤滑剤の必要性が少なく、シンプルな設計が可能。
- 耐衝撃性:繰り返し衝撃に対する耐性があり、クッション性も併せ持つ。
- 耐薬品性:多くの油脂類・アルカリに耐えるため、工業用途に適している。
ただし、吸水性があるため、水分環境下では寸法変化や物性の低下が起こる可能性があるため、定期的な点検や管理が重要です。
メンテナンスの方法と頻度
MCナイロン部品は金属部品と比較してメンテナンス頻度は少ないですが、以下のポイントを押さえることでより長寿命な使用が可能になります:
- 定期的な摩耗チェック(半年~1年に1回)
摩耗が進んでいないかを目視・寸法測定で確認。表面の摩耗溝や割れがあれば交換を検討。 - 摺動部の清掃(月1回程度)
ホコリや異物が摩擦を促進するため、エアブローや乾拭きで清掃を行う。 - 吸水状態の確認(長期稼働前・長期停止後)
湿度変化の大きい環境では、寸法変動を測定し再調整が必要な場合あり。 - 固定状態の確認(定期点検時)
ナットの緩みや締結部のがたつきが起きていないかを確認。
耐久性向上のための工夫
MCナイロンの耐久性を最大限に活かすためには、設計段階や運用中に以下の工夫を取り入れることが効果的です:
- 表面処理や含油タイプの選定
含油MCナイロン(例:オイルコンパウンドタイプ)を使用することで、潤滑性・摩耗寿命をさらに延ばすことが可能。 - 金属芯の使用
中心部に金属インサートを施すことで、剛性や耐荷重性を高めるとともに変形も抑制可能。 - 使用環境の温度管理
高温環境では熱膨張や強度低下が起こるため、連続使用温度(最大約120~130℃)を超えないように制御。 - 適切な取付方法
機械的固定やゆるみ止め構造を工夫することで、振動や荷重の繰り返しによる損傷を回避。
MCナイロンは適切なメンテナンスと運用によって、金属部品に匹敵する、あるいはそれを超える耐久性を発揮する素材です。特に回転体や摺動部品において、その性能が最大限に生かされます。
まとめ
MCナイロンは、その絶縁特性によってエンジニアにとって重要な素材です。絶縁性の高さから、電機部品や機械部品などの製造に広く利用されています。その耐久性と柔軟性も合わせて考えると、エンジニアにとっては非常に魅力的な素材と言えるでしょう。MCナイロンの絶縁特性をしっかりと理解し、適切に活用することで、製品の品質向上に大きく貢献することができます。