MCナイロンの残留応力を理解して設計精度を向上させるコツ
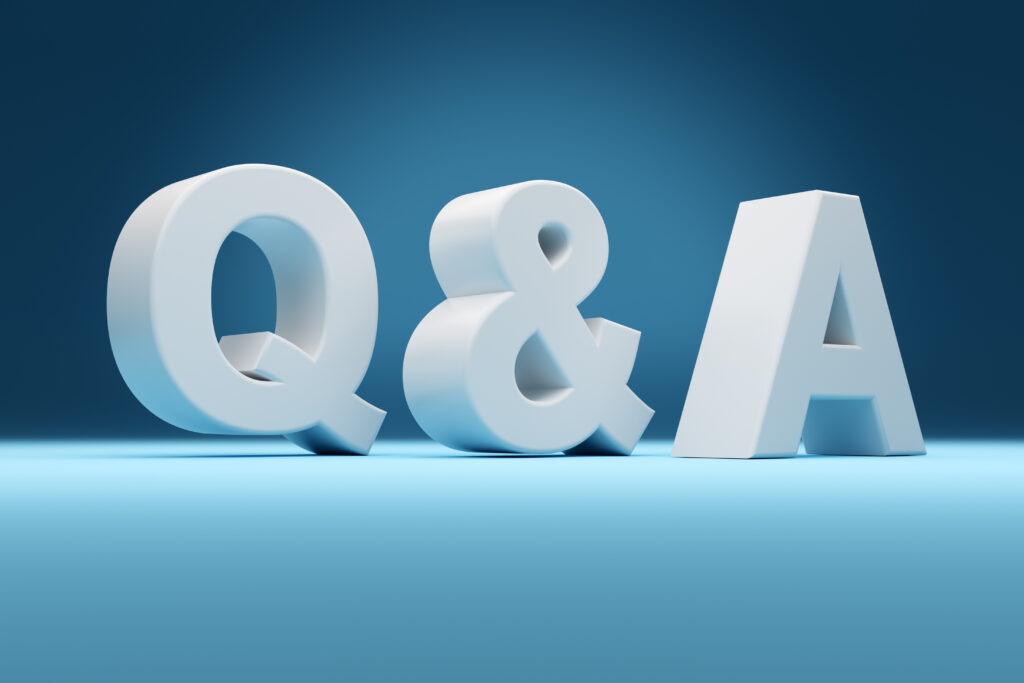
MCナイロンという素材は、様々な製品や部品の製造に広く使用されています。その中でも、MCナイロンの残留応力は設計や製造の過程で重要なポイントとなります。今回の記事では、MCナイロンの残留応力に焦点を当て、その理解を深めることで設計精度を向上させるコツをご紹介します。
MCナイロンの残留応力とは具体的に何か、そしてそれが設計にどのような影響を与えるのか。これらの疑問にお答えすることで、製品や部品の品質向上につながる重要な情報を得ることができます。設計者や製造業者の方々にとって、MCナイロンの残留応力を正しく理解し活用することは、製品の耐久性や性能向上に繋がる重要なステップと言えるでしょう。
この記事では、MCナイロンの残留応力について詳しく解説し、その理解を深めることで設計精度を向上させるためのコツを紹介します。製品の品質向上や競争力強化において、MCナイロンの残留応力の重要性を理解することは欠かせません。是非、この記事を通じてMCナイロンの素材特性について深く学び、設計の向上に役立てていただければ幸いです。
Contents
MCナイロンの基本と残留応力の概要
MCナイロン(メカニカル・コンプレッション・ナイロン)は、強度と耐摩耗性に優れたナイロン系の樹脂材料で、主に機械部品や産業用部品に広く使用されています。MCナイロンは、特に機械加工性や耐摩耗性が求められる用途において優れた性能を発揮しますが、加工中に残留応力が発生することがあります。残留応力は、製品の品質や耐久性に影響を及ぼす可能性があるため、その原因と影響について理解することが重要です。MCナイロンとは
MCナイロンは、ナイロン6(ポリアミド6)をベースにした合成樹脂で、特に機械的特性や耐摩耗性に優れています。これにより、ギアやベアリング、スライディング部品など、摩擦や負荷がかかる部品の製造に広く利用されています。MCナイロンの特長は以下の通りです:- 優れた耐摩耗性:
- 摩擦の多い部品において、高い耐摩耗性を示し、長期間の使用にも耐えます。
- 良好な機械的特性:
- 引張強度や曲げ強度が高いため、機械部品としての強度を保持します。
- 自己潤滑性:
- 摩擦係数が低く、自己潤滑性を持つため、金属と比べて摩擦を減少させます。
- 加工性:
- 軽量で加工が容易であり、精密部品の製造に適しています。
残留応力の原因と影響
残留応力は、加工中や成形中に材料内部に蓄積された応力で、加工後もそのまま製品内部に残ることがあります。MCナイロンや他の樹脂材料においても、加工や成形プロセス中に残留応力が発生します。以下の原因が残留応力の主な要因です:- 成形収縮:
- MCナイロンの成形中に、冷却や固化に伴って材料が収縮します。この収縮が不均一になると、内部に残留応力が発生します。
- 加工時の温度変化:
- 加工中に温度が急激に変化すると、熱膨張や収縮が原因で残留応力が発生することがあります。特に切削やフライス加工時に顕著です。
- 不均等な冷却:
- 成形品や加工品が冷却される過程で、外部と内部の冷却速度が異なると、材料内に不均等な応力が生じます。
- 応力集中:
- 加工中に急激な力が加わることで、応力が局所的に集中し、それが残留応力となります。
残留応力が製品品質に与える影響
残留応力は製品の機械的特性に悪影響を与える可能性があり、以下のような問題を引き起こすことがあります:- 寸法の変化:
- 残留応力が内部に残ると、時間が経つにつれて材料が自己調整を行い、部品の寸法が変化することがあります。これにより、組み立て精度が低下したり、製品の適合性に問題が生じる可能性があります。
- ひび割れや破損:
- 残留応力が大きい場合、外的な衝撃や荷重が加わると、部品が破損したり、ひび割れが生じることがあります。特に強い応力が集中している箇所では、破壊が起こりやすくなります。
- 耐久性の低下:
- 残留応力が長期間にわたって作用すると、材料の疲労強度が低下し、部品の耐久性が損なわれることがあります。
- 精度の低下:
- 加工後の部品に残留応力が残ると、使用中に微細な変形が生じ、製品の精度や機能に影響を与える可能性があります。
反りを抑制するための切削加工の工夫
反り(歪み)は、切削加工中に発生する重要な問題であり、特にプラスチックや金属などの材料において、品質や寸法精度を大きく影響します。反りを抑制するためには、加工前の材料選定、切削条件の最適化、そして切削工具の選択とメンテナンスが重要な要素となります。以下に、それぞれのポイントを詳しく説明します。加工前の材料選定
材料選定は、反りを抑制するための最初のステップです。適切な材料を選ぶことで、反りの発生を最小限に抑えることができます。以下のポイントに注意して材料を選定します:- 均一な厚みと密度:
- 材料に不均一な厚みや密度があると、加工中に収縮や膨張が不均一になり、反りが発生しやすくなります。均一な素材を選ぶことが大切です。
- 材料の応力状態の確認:
- 材料の内部に残留応力が多く含まれていると、加工中に歪みや反りが生じやすくなります。予め残留応力が少ない材料を選択し、必要に応じて熱処理を施すことが有効です。
- 熱膨張係数の考慮:
- 材料の熱膨張係数が大きいと、温度変化によって反りが生じやすくなります。特に温度変化が大きい加工環境では、熱膨張係数を考慮した材料選定が求められます。
切削条件の最適化
切削条件は反りを抑制するための重要な要素です。最適な切削条件を設定することで、材料に過剰な負荷をかけずに精度の高い加工が可能となります。以下の要素を調整することで反りを防げます:- 切削速度と送り速度の調整:
- 高すぎる切削速度や送り速度は、加工中に過剰な熱を発生させ、材料に応力がかかりやすくなります。適切な切削速度と送り速度を選定し、熱の蓄積を抑えることが重要です。
- 深さの調整:
- 一度に大きな切削深さを取ると、材料に過剰な負荷がかかり、反りや歪みが発生することがあります。浅めの切削を複数回行うことで、反りを抑制できます。
- 冷却の最適化:
- 切削中の冷却が不十分だと、局所的に高温が発生し、反りが生じる原因になります。適切な切削液を使用し、冷却状態を最適化することで、熱の影響を抑えることができます。
切削工具の選択とメンテナンス
切削工具の選定とそのメンテナンスも反りを抑制するために重要です。適切な工具を選ぶことで、切削中の摩擦や熱の発生を抑え、材料にかかる応力を最小限に抑えることができます:- 適切な工具の選定:
- 材料の特性に合った切削工具(刃物やフライス工具など)を選定することが重要です。例えば、プラスチック系の材料には鋭利な工具を、金属系の材料には耐摩耗性の高い工具を選びます。
- 工具の切れ味の保持:
- 鋭利な工具は切削時に発生する熱を抑制し、材料にかかる圧力を減少させます。定期的なメンテナンスや研磨を行い、工具の切れ味を保持することが重要です。
- 工具の摩耗管理:
- 切削工具が摩耗すると、切削の精度が低下し、加工中に反りが生じやすくなります。工具の摩耗を管理し、定期的に交換または研磨を行うことで、安定した加工を維持できます。
樹脂切削の公差マスタリング
樹脂切削加工において、製品の精度を維持するためには公差設定が重要な要素となります。特にMCナイロンのような樹脂材料は、その特性に応じた公差の管理が必要です。以下では、公差基準の理解、MCナイロンの加工特性、公差精度を高めるためのポイントを詳しく説明します。公差基準の理解
公差とは、製品の寸法が許容される範囲を指し、製品が求められる機能を満たすために必要な精度を設定するものです。樹脂の切削加工では、材料の性質、加工条件、使用する工具によって公差の管理が難しくなることがあります。公差基準を理解するために、以下の点に留意することが大切です:- 公差範囲の定義:
- 公差は、加工対象の寸法とその許容誤差を明確に定義するものです。たとえば、寸法が50mm±0.05mmという場合、50mmの中心から±0.05mmの範囲で加工されることを意味します。
- 公差の階級設定:
- 樹脂加工においては、必要な精度を基に適切な公差階級を設定します。高精度が要求される部品には厳しい公差が必要となりますが、一般的には樹脂加工では±0.1mm~±0.5mm程度が多いです。
- 設計と加工の調整:
- 公差基準を設計段階で適切に決定し、加工条件と合わせて調整します。特に樹脂素材の場合、変形や収縮の影響を受けやすいため、設計段階での公差の柔軟性が重要です。
MCナイロンの加工特性と公差
MCナイロン(メカニカルコンパウンドナイロン)は、強度、耐摩耗性、耐熱性に優れる材料ですが、加工においてはいくつかの特性が公差設定に影響を与えます:- 熱膨張と収縮:
- MCナイロンは温度変化による膨張や収縮があるため、切削中に熱による寸法変化が生じます。この特性により、切削後の冷却過程で寸法が変化する可能性があるため、公差設定を緩めるか、冷却管理を徹底する必要があります。
- 剛性と摩耗性:
- MCナイロンは強度が高く、耐摩耗性に優れていますが、その硬度が切削工具に対する負担を大きくすることがあります。これにより、工具の摩耗や熱の発生が精度に影響を与えるため、工具の選定や切削条件を工夫することが求められます。
- 加工中のひずみ:
- MCナイロンは加工中に変形やひずみが発生しやすいため、加工後に寸法が変化する可能性があります。これにより、反りや歪みが発生し、精度が低下することがあります。これを避けるためには、適切な切削条件と冷却方法を採用することが大切です。
精度を高めるためのポイント
MCナイロンを使用した切削加工において、高精度を実現するためには以下のポイントに注意を払いながら加工を行うことが重要です:- 適切な切削速度と送り速度:
- 切削速度や送り速度が過度に速すぎると、熱が発生し、収縮や変形が生じやすくなります。適切な速度を設定することで、熱の影響を最小限に抑え、精度を保つことができます。
- 冷却液の使用:
- MCナイロンは熱に敏感なため、適切な冷却液を使用して、切削中の温度上昇を抑えることが重要です。これにより、収縮やひずみの発生を防ぎ、精度を高めることができます。
- 工具の選定とメンテナンス:
- 高精度を維持するためには、工具の切れ味を常に保つことが重要です。工具の摩耗を最小限に抑えるために、定期的なメンテナンスを行い、工具交換を適切に実施します。
- 微細な切削加工の実施:
- MCナイロンを高精度で加工するためには、微細な切削加工を複数回行うことが効果的です。大きな切削深さを一度に取るのではなく、少しずつ削ることで、反りや歪みを抑えることができます。
MCナイロンとPOMの材料比較
MCナイロン(メカニカルコンパウンドナイロン)とPOM(ポリアセタール)は、いずれも広く使用されているエンジニアリングプラスチックです。それぞれが持つ特性に違いがあり、利用シーンや設計要件に応じて材料を選定することが重要です。以下に、MCナイロンとPOMの特性、利用シーンに応じた材料選定、および設計者が考慮すべき選定ポイントを説明します。MCナイロンとPOMの特性
- 強度 MCナイロンは高い強度と耐荷重性を持つ一方、POMは高い引張強度と圧縮強度を誇ります。
- 耐摩耗性 MCナイロンは非常に優れた耐摩耗性を持っており、POMも良好な耐摩耗性を示しますが、MCナイロンが特に優れています。
- 耐熱性 MCナイロンは高い耐熱性(100〜120℃)を有し、POMは中程度の耐熱性(80〜100℃)があります。
- 耐薬品性 MCナイロンは酸やアルカリに対する耐性が良好で、POMは一部の化学薬品に強いですが、MCナイロンが全体的に優れています。
- 加工性 両者ともに加工が容易ですが、MCナイロンは特に機械的加工性に優れており、POMは精密な加工が可能です。
- 水分吸収率 MCナイロンは中程度の水分吸収率を示し、湿気に影響されやすいのに対し、POMは低い水分吸収率を持ち、湿気の影響を少なくします。
- 音響特性 MCナイロンは低音響特性があり、静音性が良いのに対し、POMは比較的騒音が高めです。
利用シーンに応じた材料選定
- MCナイロン MCナイロンは、摩耗性が重要な部品や衝撃に耐えられる部品、高温環境で使用される部品に適しています。例えば、ギア、ベアリング、スライディング部品などに使用されます。
- POM(ポリアセタール) POMは精密部品に適しており、特に低摩擦が求められる部品(例:精密ギアやプーリー)に最適です。また、低温でも性能が安定しており、冷却装置や車両部品にも使用されます。
設計者が考慮すべき選定ポイント
- 耐摩耗性 高い耐摩耗性が求められる部品には、MCナイロンが適しています。特に、長期間使用する部品においては、MCナイロンが有効です。
- 強度と荷重 強度が重要な部品には、POMが有効です。特に、軽量でありながら高強度が求められる場合、POMが適しています。
- 耐熱性 高温環境での使用が求められる場合、MCナイロンの方が優れています。耐熱性が100℃以上の範囲が必要な部品に最適です。
- 寸法安定性 精密部品の設計にはPOMが最適です。寸法安定性と低摩擦係数を持つPOMは、精密機械部品に向いています。
- 湿気や化学薬品への耐性 MCナイロンは湿気に影響を受けやすいものの、化学薬品への耐性が優れています。POMは湿気への影響が少なく、長期間安定した性能を発揮します。
樹脂加工品のアニール処理
アニール処理は、樹脂加工品の内部応力を解消し、物性を安定させるための重要な工程です。特に、MCナイロンやその他のエンジニアリングプラスチックにおいては、アニール処理によって性能向上や品質の保持が可能になります。以下では、アニール処理の目的と効果、MCナイロンのアニール方法、そしてアニール処理後の品質保持について詳しく説明します。アニール処理の目的と効果
- 内部応力の解消 樹脂加工品は成形時や加工中に内部応力が発生することがあります。アニール処理によって、この内部応力を解消することで、寸法安定性が向上し、ひずみや反りを防止することができます。
- 材料特性の安定化 アニールによって樹脂の分子構造が再編成され、材料の物性が安定します。これにより、後工程での品質が安定し、成形品の信頼性が向上します。
- 強度や耐摩耗性の向上 アニール処理により、MCナイロンのような樹脂の強度や耐摩耗性が向上し、使用条件に対する耐久性が高まります。
- 寸法精度の向上 樹脂製品の熱膨張を制御し、アニール後に寸法精度が向上するため、特に精密部品において重要な処理となります。
MCナイロンのアニール方法
- アニール温度の設定 MCナイロンの場合、アニール温度は約100〜120℃の範囲で設定するのが一般的です。温度が高すぎると樹脂が劣化するため、温度管理が重要です。
- アニール時間の調整 アニール時間は製品のサイズや厚み、使用されている材料の状態によって異なりますが、通常は数時間から数十時間にわたる加熱が必要です。均一な温度管理を行うことが、アニール処理の効果を最大化します。
- 冷却方法 アニール後の冷却は徐々に行うことが重要です。急激な冷却は新たな応力を生じさせる可能性があるため、自然冷却または制御冷却が推奨されます。
アニール処理後の品質保持
- 寸法安定性 アニール処理後は、製品が環境や使用条件に応じて安定した寸法を保持することができます。これにより、精密機器や部品の使用において高い信頼性を提供します。
- 強度と耐久性の確保 アニール処理により、MCナイロンなどの樹脂は強度や耐久性が向上し、長期間の使用に耐えることができます。摩耗や荷重に対する耐性も強化されます。
- 反りやひずみの防止 アニール処理により、加工品の反りやひずみが減少し、製品が所定の形状を保つことができます。特に薄肉の部品や精密部品では、この効果が顕著です。
- 品質の一貫性 アニール後の製品は、熱的・機械的な安定性が向上し、長期にわたって均一な性能を維持します。これにより、生産ラインでの品質が一貫して高く保たれます。
プラスチック切削時の残留応力緩和方法
プラスチック切削加工では、残留応力が発生しやすいことがあり、この残留応力が後工程での製品の形状変化や性能低下を引き起こす原因となります。残留応力を効果的に緩和するための方法を理解し、適切な対策を講じることが重要です。以下では、残留応力の概要、測定方法、そしてその緩和技術について詳しく説明します。残留応力とは
残留応力は、加工や成形時に材料内部に残る応力で、外部の力が加わっていない状態でも存在します。プラスチックの切削加工や成形時に、急激な温度変化や不均一な冷却などが原因となり、材料内部に応力が蓄積されることがあります。この残留応力は製品の寸法精度に悪影響を及ぼし、変形や反り、ひずみを引き起こすことがあります。残留応力の測定方法
残留応力を正確に把握することは、緩和方法を選定するために重要です。以下の方法で残留応力を測定できます。- X線回折法 X線回折法は、材料内部の結晶構造の変化を測定することで残留応力を評価する方法です。高精度で非破壊的に測定できるため、広く利用されています。
- 応力測定テスト 紙のような薄い材料を使用して、応力の変化を測定します。特に精密部品の測定に適しています。
- ホールドリル法 一定の深さまで穴をドリルで開け、残留応力がその深さでどう変化するかを観察します。主に厚物部品に用いられる方法です。
- レーザー反射法 レーザー光を利用して、材料の表面に加わる応力の影響を測定します。この方法は、薄い材料の応力測定に有効です。
残留応力を緩和する加工技術
残留応力を緩和するためには、以下の加工技術が有効です。- アニール処理 アニール処理は、材料を適切な温度に加熱し、その後ゆっくりと冷却する方法です。これにより、内部の応力が解放され、材料の物性が安定します。アニール処理は特に熱可塑性樹脂やエンジニアリングプラスチックに効果的です。
- 均一な冷却 加工後の冷却を均一に行うことで、応力の集中を防ぎます。急冷や局所的な冷却を避け、自然冷却や温度制御冷却を採用することが推奨されます。
- 低速切削加工 切削速度を遅くすることで、加工中に生じる熱の発生を抑え、残留応力の生成を減少させます。また、切削中の温度差を減らすことで、加工後の変形を防止することができます。
- 振動加工の利用 振動を利用して材料を微細に加工することで、応力を均等に分布させ、内部応力の蓄積を防ぐことができます。
- 最適な切削条件の設定 切削条件(切削速度、送り速度、刃具形状など)を最適化することで、加工中に発生する熱や応力を管理し、残留応力の発生を抑えることができます。
- プレ加工(プレストレスト加工) 加工前に特定の応力を材料に加えることによって、最終的な製品における応力の発生を減少させる技術です。この方法は、特に複雑な形状を持つ部品の製造に有効です。